On January 5, 2024, an Alaska Airlines Boeing 737 MAX 9 made global headlines, when a door plug blew off while the aircraft was inflight. This has caused the FAA to ground the Boeing 737 MAX 9, as regulators are investigating what happened.
Given the Boeing 737 MAX’s history, there have been a lot of questions about what caused this incident. Is there a bigger issue with the 737 MAX 9, or how could a door just blow off while inflight? Well, it looks like we now have our answer.
In this post:
Boeing forgot to install bolts on 737 MAX 9 door plug
Dominic Gates at The Seattle Times has a great scoop on what reportedly happened to cause this incident, per an industry source. According to this source, the panel that blew off the Alaska Airlines 737 MAX 9 had been removed for repair and then reinstalled incorrectly by Boeing mechanics at the final assembly line in Renton, Washington.
If this ends up being confirmed (it hasn’t been officially confirmed by Boeing or the NTSB), it would of course mean that Boeing is fully at fault here. Prior to this, there were questions of whether Boeing or Spirit Aerosystems was behind the issue, with the latter being the company that manufactures many components of the jet.
So, how did Boeing incorrectly reinstall the door plug? According to a whistleblower, the company’s own records show that four bolts “were not installed when Boeing delivered the airplane.”
Work like this is supposed to be signed off on by Boeing quality inspectors, so how did this slip through the cracks? Boeing reportedly has a process failure whereby it uses two separate systems to record what work has been completed.
The whistleblower states that “the reason the door blew off is stated in black and white in Boeing’s own records” and that “it is also very, very stupid and speaks volumes about the quality culture at certain portions of the business.” Boeing’s 737 production system is also described as a “rambling, shambling, disaster waiting to happen.”
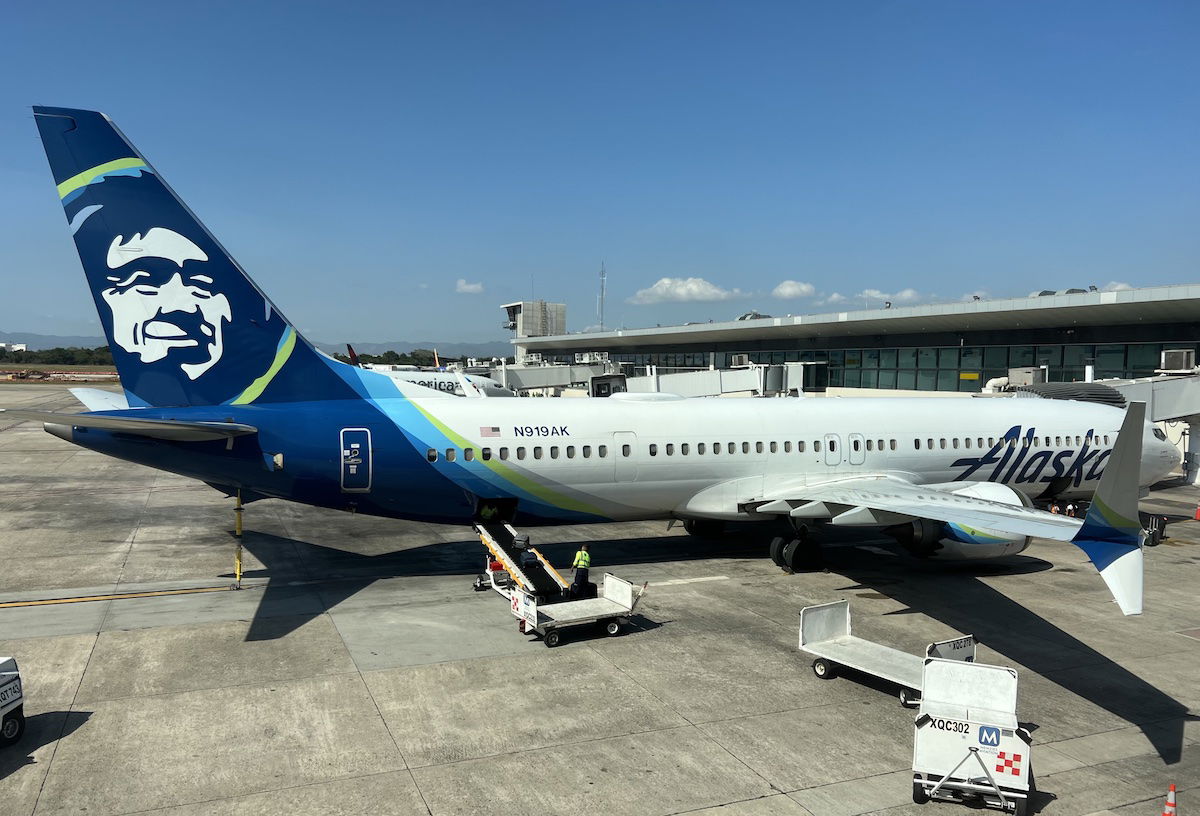
I’m not sure if this is a good or bad update
Assuming all of this checks out, I’m not sure what to make of this. On the one hand, it would be good news if there weren’t actually an additional, consistent problem with the 737 MAX, but rather there was an error that can easily be traced.
On the other hand, how the heck does an aircraft manufacturer have a process in place whereby a repair is performed, four bolts are missing, and there are no quality control measures in place? How is that even remotely excusable for a company that is the United States’ largest exporter, and which has been producing planes for decades? And how is it possible that this is the process after Boeing got so much scrutiny regarding the 737 MAX, after it was grounded for nearly a couple of years?
There are still quite a few questions, though. For example, 737 MAX 9 operators performed inspections on aircraft following the incident earlier this month, and many found loose bolts. Are those loose bolts normal, since that seems to be different than this situation, where the plane was just missing four bolts?
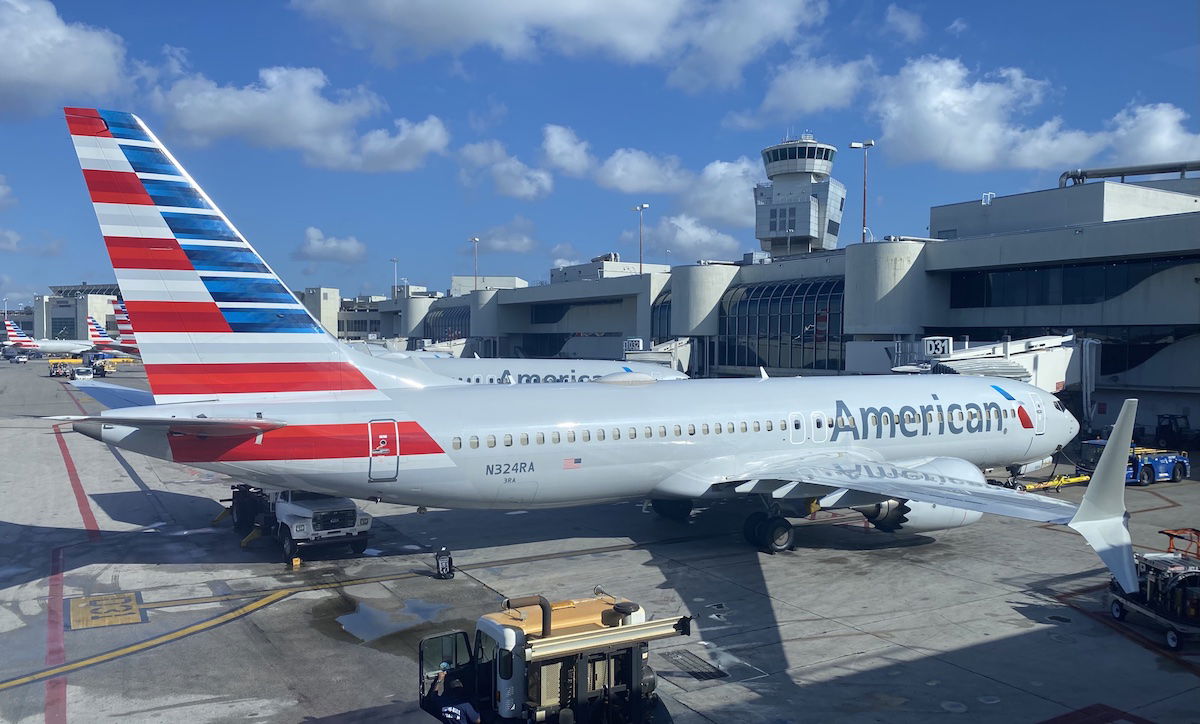
Bottom line
With Boeing 737 MAX 9s being grounded at the moment, the goal is to figure out what caused the recent incident on an Alaska 737 MAX 9. The latest update seems to be that Boeing had tried to perform a fix on this particular door, but mis-installed it, leaving out four bolts. While there are supposed to be quality checks in place, those just didn’t happen, due to Boeing reportedly using two different systems.
I’m sure this will all be officially verified one way or another soon. I can’t decide if it’s reassuring to think that there’s not a bigger issue with the aircraft, or terrifying to think that Boeing’s quality control is so poor.
What do you make about this alleged cause of the 737 MAX 9 incident?
The United States has a major trade gap. Boeing being the country’s largest exporter will be protected at all costs. How that happens remains to be seen, but I would bet on the politics of that situation prevailing.
That is not acceptable to not have an inspection prior to covering the plug with insulation and sidewall.
Where I worked anytime work was accomplished that would be covered it was mandatory that an inspector was required to verify all work was complete before covering in that entire area..
U can always do radiographic inspection of covered areas before sign off. Also there should be video record of spaces before any space is covered up with next stage material. Boeing is stupid.
Stop hiring accountants to run Boeing. Ever since the merger with MD, true engineers stopped driving the ship and accountants have RUINED a once great company. Boeing needs to get back to solid science backing it's decision making and NOT the bottom line.
Presumably the FAA gets tips to pass things. So thats not a fix.
Probably a fix, which I would not like, but in practicality, the Chinese will buy Boeing and fix it.
What the whistleblower report speaks to, which has now btw been corroborated by enough other sources so that it is making national news (Seattle Times, but also NY Times, WSJ, etc,) is that there are systematic process failures in Boeing's manufacturing execution and quality management system. This is an enormous problem!
The person or persons who failed to install the bolts and inspect the work should be fired!
When will those in the media, especially the aviation media, start calling out Spirit Aerosystems for what it is? Boeing built them up to outsource union labor to non-union shops and outsource liability. How many layoffs did Boeing have during COVID? Few. Spirit? Thousands. Why? Because Spirit is non-union and builds the majority of the plane. Boeing is nothing more than a higher-level assembly facility. Strategic move by Boeing. Let’s call it out for what it is.
sorry but your statements are wrong.
Spirit is unionized. Did you forget the strike they had last summer that stopped 737 production?
The door plug was produced in Malaysia by yet another subcontractor.
And Spirit has had quality problems and the door plug that failed was removed by Boeing and then reinstalled but incorrectly.
This is Boeing's problem. They ultimately deliver the final product and their processes have to ensure that whatever work...
sorry but your statements are wrong.
Spirit is unionized. Did you forget the strike they had last summer that stopped 737 production?
The door plug was produced in Malaysia by yet another subcontractor.
And Spirit has had quality problems and the door plug that failed was removed by Boeing and then reinstalled but incorrectly.
This is Boeing's problem. They ultimately deliver the final product and their processes have to ensure that whatever work subcontractors do is made right before letting a plane go out for delivery
To be totally fair, Boeing created the Spirit issue by pushing on prices and payment terms. You get what you pay for. And no QC is perfect, quality-by-design is much more powerful. The less mistakes you have to correct the less you have a chance to miss one (which was the case here).
What is described is a culture (at Spirit) of delivering sub-spec parts to coaxe profitability out of the too tight financial terms...
To be totally fair, Boeing created the Spirit issue by pushing on prices and payment terms. You get what you pay for. And no QC is perfect, quality-by-design is much more powerful. The less mistakes you have to correct the less you have a chance to miss one (which was the case here).
What is described is a culture (at Spirit) of delivering sub-spec parts to coaxe profitability out of the too tight financial terms from Boeing and hoping Boeing does not notice or care enough to have it fixed by Spirit on their own dime.
And Boeing despite knowing Spirit has too high rate of errors does nothing to address the rootcause, because it's (short-term) financially better to fix errors than to prevent them. (And take the risk that one escapes your sight and has dramatic consequences).
Spirit also supplies Airbus, I wonder if the same issues happen?
If so, have they taken the route to systematically correct what comes from Spirit ? Or are the financial terms simply more comfortable and allow Spirit to have properly trained staff and properly staffed QC ?
On the Spirit side, is this a site related issue (Wichita only) ? This would explain why the other Spirit sites (which I assume are rather the ones supplying Airbus) do not have as much rework problems.
first, Airbus builds a higher percentage of its planes' own content itself than Boeing does.
and Airbus doesn't have the problems that Boeing has because they demand more of their suppliers
Subcontracting does not have to be a death sentence for quality if it is managed properly.
Boeing isn't willing to do what is necessary to make sure that its suppliers deliver the quality Boeing needs - and then Boeing doesn't deliver...
first, Airbus builds a higher percentage of its planes' own content itself than Boeing does.
and Airbus doesn't have the problems that Boeing has because they demand more of their suppliers
Subcontracting does not have to be a death sentence for quality if it is managed properly.
Boeing isn't willing to do what is necessary to make sure that its suppliers deliver the quality Boeing needs - and then Boeing doesn't deliver the quality with its own processes that Airbus does.
And let's not forget that Spirit is a global company and some of its plants for Airbus are not even in the US.
pretty stunning slip up and how anybody can have confidence in this plane now is beyond me. they need to put them all thru D check and do a complete nose to tail inspection to make sure other parts aren't ready to fall off. It is only by luck that the door didn't hit the tail when it blew out - had that happened, it would have jammed the stab and crashed into a populated area. Whole executive leadership should be fired and bonuses clawed back.
And Boeing wants more safety waivers. They are a joke. Maybe I should sell my remaining shares.
The MAX 9 will be back in service this weekend, first by Alaska and then by United on Sunday.
Curious. With all airplanes operating full these days was that a coincidence that row of seats were empty, of was there some suspicious reason with previous air leaks in that area?
Apparently the 2 passengers destined fo rthe row were late or misconnected.
Wow, I was going to give Alaska some credit for Not seating pax in that roŵ after they failed to identify the cause of THREE Air Pressure warning in that cockpit but continued to fly that jet. The 2 pax that missed the flight better count their 9 lives. Alaska could've easily had a much worse issue on their hands for failing to FIND the cause of those very valid AIR PRESSURE WARNING LIGHTS, 3...
Wow, I was going to give Alaska some credit for Not seating pax in that roŵ after they failed to identify the cause of THREE Air Pressure warning in that cockpit but continued to fly that jet. The 2 pax that missed the flight better count their 9 lives. Alaska could've easily had a much worse issue on their hands for failing to FIND the cause of those very valid AIR PRESSURE WARNING LIGHTS, 3 times the jet, Boeing, was telling Alaska this jet was NOT AIR TIGHT, should have grounded the plane. Boeing is still at FAULT for failing to install those 4 critical bolts and cutter pines. By design, those bolts have kept the plug doors in place for many DECADES. AT LEAST we can now remove the possibility of another Design Flaw, Just poor human assembly quality and lack of inspections by Boeing which the new Management team promised to Improve!
I'm old enough to remember "if it's not Boeing I'm not going"..... Now it's "if it's Boeing I need to rethink if I'm going". UNACCEPTABLE.
Considering that majority of WMDs are made by Boeing. Weapon delivery platforms are built by Boeing.
Who do you think build the planes that dropped nukes in Japan, dropped napalms in Vietnam, bombed Afghan and the Gulf or all the current active land based nuclear weapons, more than capable of ensuring mankind extinction.
They're pretty much in the business that doesn't try to keep you alive.
If it's not Boeing it's not exploding.
People did not do their job and need to be fired
Who fires the CEO?
in well-run companies, the board should do that if necessary.
I was trying to imply that at Boeing, that's apparently no one, but maybe I was too subtle.
I have to assume Calhoun's strategy did not only come from himself, but was infused/supported by the Board.
Sure, he can be used as a fuse, to protect the Board from their poor decisions, but in my view, it's the Board who has a problem. They appointed him, an accountant. And who fires the Board ? To a large extent the Shareholders.
As long as all those issues don't translate to sustainably and...
I have to assume Calhoun's strategy did not only come from himself, but was infused/supported by the Board.
Sure, he can be used as a fuse, to protect the Board from their poor decisions, but in my view, it's the Board who has a problem. They appointed him, an accountant. And who fires the Board ? To a large extent the Shareholders.
As long as all those issues don't translate to sustainably and obviously bad financial performance (especially in comparison to competition), that cannot be blamed on externalities (like KC46 or Airforce One contracts) I see no reason for a change of expectation from Shareholders, cascading to Board, to CEO and to Company, and thus I expect no change of culture.
Will that come soon enough before customers withdraw orders and push the company to bankruptcy ? When does it become a better deal for an airline to keep old generation aircraft than hope your suppliers delivers the late planes you are waiting for (and the compensation planes they promised you for being late) ?
Having worked for several high tech companies I can say from experience: technology companies cannot be safely run by MBAs, it requires engineers, and good ones at that. Fire the businessmen, promote the crustiest engineers, endure delays in support of quality, and watch the long term success.
Having worked for several high tech companies I can say from experience: technology companies without MBAs would be acquired by companies run by MBAs.
Having been in technology companies run by engineers for 15+ years, it takes a village. I remember specifically all the engineers in my MBA program and thinking, wow, these folks have no practical business knowledge at all. Engineers should be engineers. Business people should be business people.
I 100% agree with you, aviation is not going to operate safely with MBA’s running a company and farming out work to the lowest bidder, still it’s inexcusable not to have installed the bolts or an inspector to catch it.
Someone, likely a mechanic / builder knows the truth about the bolts not being installed. Follow the paperwork it always tells the truth. Sometimes by omission of the facts.
We need to stop saying door plug. It isn't a door plug. It's a door, full stop.
Sorry, I meant self-opening door. It's got springs to force itself open when closed unless you put bolts in.
That wouldn't be accurate.
Boeing gives three options for an F-type entrance: an activated door, a deactivated door, and a plug.
This was a plug.
Wrong. They *CALL* it a plug in their sales material, but it is *NOT AT ALL* a plug. It is a fully operational door that is covered over by the interior.
A plug is something that is bigger than the hole it is meant to fill. What Boeng installs in place of a normally fully functional door is... a door. One that is spring-loaded to open.
Even the FAA call it a door plug rather than a door. Maybe it is a door plug after all....
https://www.faa.gov/newsroom/updates-grounding-boeing-737-9-max-aircraft
...again... what you just described, is the second of three options listed above.
That's not the only alternative within that space, to a functioning door.
New board and urgent 797 plans needed, to replace not only 737 but also the lost 757 and 767 mid market family.
Another decade is too long on this over developed 1967 plane. The 747 nearly broke Boeing, but they had to risk it. The fact they are saying the tech isn’t ready for a new frame shows they still don’t get it, it is about the basics being right Ona reliable, affordable new model not necessary ultra tech.
the fastest way to force Boeing to move on from the 737 is to tell them that the FAA will not grant any more exemptions for any safety systems that should be on all new models but which do not exist on the MAX.
It's time for Boeing to do a hail Mary to save the company and their reputation and build an all new aircraft. and do it right. Something they didn't do with the 787 or with the MAX
The FAA did just say that it will not allow Boeing to increase its production rate until its quality is improved.
If they can’t build a plane that they be building for fifty years what makes you think they can build an entirely new aircraft with any quality. Just look at their military and NASA divisions which are also disasters.
Boeing has an incredibly tight process control system. The issue here is that someone went outside that system in an event where atypical work was needed. How to handle that work wasn't defined. One has to wonder if there was a culture where the person felt the need to hide that rework to avoid getting in trouble, but still, the way to catch this is to build more robust automation. The CMES system could have...
Boeing has an incredibly tight process control system. The issue here is that someone went outside that system in an event where atypical work was needed. How to handle that work wasn't defined. One has to wonder if there was a culture where the person felt the need to hide that rework to avoid getting in trouble, but still, the way to catch this is to build more robust automation. The CMES system could have logic added that says "a door part was removed...there needs to be a corresponding quality check on the associated part".
But I think it's important not to paint Boeing as a company that's "a shambles". It's common for mechanics to bitc* and moan like this because they'd rather be fishing than working. That will never change no matter how good the processes are. Boeing just needs to add a little more robust logic to its quality check systems.
The problem is no matter how tight the "sieve" is, when you feed it mostly clear water, clearer water comes out. But when you feed it mud, it plugs, overflows or fails.
And Boeing has cornered Spirit in feeding them "mud", because that's the only thing they were willing to pay for.
So yes, there is a culture issue at Boeing, not in terms of the technical capability of the people doing technical...
The problem is no matter how tight the "sieve" is, when you feed it mostly clear water, clearer water comes out. But when you feed it mud, it plugs, overflows or fails.
And Boeing has cornered Spirit in feeding them "mud", because that's the only thing they were willing to pay for.
So yes, there is a culture issue at Boeing, not in terms of the technical capability of the people doing technical work, but in the amount of money the company is willing to pay to deliver on what it committed to.
It can be how little they pay suppliers, or how junior the technicians on the shop floor are, or how little quality control staff they hire, or how much they put pressure on fast delivery or how small a development budget they allocate. Or all of the above, who cares ?
All amount to the same result: people cut corners, knowingly or not, willingly or not. And plugs fly off.
A bit odd to have a picture of American Airlines considering they don't fly the MAX-9
The market would suggest this is a "good" update, since Boeing shares are up.
I'll wait for final reports. A lot of times paperwork is incomplete or incorrect. A big part of the problem with this plug component, is it's a "door" that is hidden behind panels. A proper door if it had bolts missing or working loose, you'd see that as it's in use. Hidden components like this should require triple inspection and photographic/video records not just paperwork, prior to being covered up with plastic.
Easy to say. The issue is that this door WAS double checked.
And then it was removed...
but in the system the removal was called "opened" (probably by analogy to non-plug emergency exits).
An "opening" of the door (which for a plug is same as removing it) does not trigger an additional checklist to make sure it's properly reinstalled. A "removal" does. So "removal" is less fast than "opening", which matters when...
Easy to say. The issue is that this door WAS double checked.
And then it was removed...
but in the system the removal was called "opened" (probably by analogy to non-plug emergency exits).
An "opening" of the door (which for a plug is same as removing it) does not trigger an additional checklist to make sure it's properly reinstalled. A "removal" does. So "removal" is less fast than "opening", which matters when you are under a lot of pressure.
So you have multiple causes:
- Wrong installation of a gasket and some rivets by Spirit that led to removing of a properly bolted plug door
- the removal was quite late in the assembly process as Spirit has to do the repair work and is overloaded/losing money, so does not do this very willingly
- due to late fixing everyone was very stressed under a lot of pressure to make things moving fast
- Quality system did not identify that opening and removing a PLUG door are the same operation, requiring reassembly checklist, contrary to regular emergency exits which can be opened and closed easily.
- Technicians under a lot of pressure used this loophoole to please management to be faster to put the plane in service
- No cross-check was formally required as, in the system, the door had properly been installed and never "removed"
Devil is in the details and just calling for a triple-check will not help. Making sure the subcontractor is paid appropriately to be able to deliver compliant parts and make a profit and fix rare escapes in a timely manner would have prevented this issue.
Making sure enough time is allocated to see that plug doors need special procedures and quality checks is another one.
All of that amounts to more $$$ required to build one plane and less $$$ in management and shareholders pockets.
An interesting video on an AirChina 738.
https://twitter.com/Byron_Wan/status/1545015313724346368?s=20
I'm at a loss to find the exact reason for the door to have been designed at all, as I've been unable to find a single instance of *any* airline leaving the door unplugged. If an architect designed a building with every apartment having a door that was covered up...wouldn't they rethink the design?
It's because a high-density layout would max out the exit capacity before the plane bulks out. United and Alaska, with their first class cabins, do not go past the 189 limit of the -800 exit configuration. Lion Air, the Indonesian LCC, does. Look at pictures of their planes. They have a tiny porthole in the same place. That is the actual door, not the full-size window that the blank has.
I seem to recall Continental Airlines having that door on it's 737-900ER's.
I wonder if they are still at UA, post merger.
Lion air uses the door configuration.
As stated by others, Lion Air does, on the 737-9s.
Ryanair, Buzz, Air Malta, Akasa Air, and Allegiant will use it on the 737-8200.
Lion Air had the same configuration on their 737-900ERs which is why some of Delta's newly acquired used ex-Lion Air aircraft have an active set of emergency doors where other 739s have plugs.
If the missing bolts really is the issue then the newly discovered loose nuts are a different problem that was identified by this investigation. I'd bet that if you analyzed each plane as minutely as this, even Airbus planes, you'd find similar things. But would it kill the design to just add some lock washers???
The door design is bad, period. They literally have springs on the bottom hinges trying to force the door open at all times. Something goes wrong (like forgetting to put the bolts back, which is a silent error) and that door is going to open itself eventually.
Compare that to a regular airline door, which is fail-safe closed. If it's closed, it is absolutely going to stay that way at altitude, because on regular...
The door design is bad, period. They literally have springs on the bottom hinges trying to force the door open at all times. Something goes wrong (like forgetting to put the bolts back, which is a silent error) and that door is going to open itself eventually.
Compare that to a regular airline door, which is fail-safe closed. If it's closed, it is absolutely going to stay that way at altitude, because on regular aircraft doors if it closed, then it is going to stay that way at altitude, there's no close AND THEN lock. Because people forget steps, and you can't rely on people remembering to do something.
On the fake doors, it may LOOK closed, but not actually be secured to stay closed at altitude. That is just plain bad design.
The MAX-9 should stay grounded until they redesign the hidden doors.
This is the exact same design that was used in the 737-900ER, years of service without incident
I'm sure all of the victims of airplane accidents due to mechanical defects are comforted that the design that failed had previous years of service without incident.
Lots of things are fine until they are not. In this case, it's fine, as long as the bolts are properly installed.
Sometimes, apparently they are not, and then the door blows out at altitude.
Designs that are acceptable in many environments are simply not acceptable on airplanes,...
I'm sure all of the victims of airplane accidents due to mechanical defects are comforted that the design that failed had previous years of service without incident.
Lots of things are fine until they are not. In this case, it's fine, as long as the bolts are properly installed.
Sometimes, apparently they are not, and then the door blows out at altitude.
Designs that are acceptable in many environments are simply not acceptable on airplanes, even if they work almost all of the time. This door has a single point of failure (forgetting to put the bolts in), and single points of failure on airplanes are not acceptable. Especially single SILENT points of failure.
Do you really think the Spring is the reason the door blew open? It doesn’t matter what kind of design panel you install on an airframe, if it isn’t secured correctly, it is going to eventually blow out when the plane is pressurized. The fact that the door plug stayed in place for so long despite bolts being entirely missing is a testament to the quality of the design, and the shoddiness of the manufacturing quality
Interesting the plane in question was assembled at Boeing's Renton plant. The popular wisdom has always been that defective aircraft came from the non-unionized, unskilled, and red neck workers at the Charleston plant. I am waiting for apologies from all the smug west coasters who for years smeared the hardworking Boeing employees in SC.
They're even worse
Maximizing shareholder value. Boeing's overriding passion.
Ben, the source is from a Leheem News Article- “Unplanned” removal, installation inspection procedure at Boeing, comments section, therefore, cannot be verified.
throwawayboeingN704AL- (16/01/2024)
https://leehamnews.com/2024/01/15/unpla ... ent-509962
'Current Boeing employee here – I will save you waiting two years for the NTSB report to come out and give it to you for free: the reason the door blew off is stated in black and white in Boeings own records. It is also...
Ben, the source is from a Leheem News Article- “Unplanned” removal, installation inspection procedure at Boeing, comments section, therefore, cannot be verified.
throwawayboeingN704AL- (16/01/2024)
https://leehamnews.com/2024/01/15/unpla ... ent-509962
'Current Boeing employee here – I will save you waiting two years for the NTSB report to come out and give it to you for free: the reason the door blew off is stated in black and white in Boeings own records. It is also very, very stupid and speaks volumes about the quality culture at certain portions of the business.
A couple of things to cover before we begin:
Q1) Why should we believe you?
A) You shouldn’t, I’m some random throwaway account, do your own due diligence. Others who work at Boeing can verify what I say is true, but all I ask is you consider the following based on its own merits.
Q2) Why are you doing this?
A) Because there are many cultures at Boeing, and while the executive culture may be throughly compromised since we were bought by McD, there are many other people who still push for a quality product with cutting edge design. My hope is that this is the wake up call that finally forces the Board to take decisive action, and remove the executives that are resisting the necessary cultural changes to return to a company that values safety and quality above schedule.
With that out of the way… why did the left hand (LH) mid-exit door plug blow off of the 737-9 registered as N704AL? Simple- as has been covered in a number of articles and videos across aviation channels, there are 4 bolts that prevent the mid-exit door plug from sliding up off of the door stop fittings that take the actual pressurization loads in flight, and these 4 bolts were not installed when Boeing delivered the airplane, our own records reflect this.
The mid-exit doors on a 737-9 of both the regular and plug variety come from Spirit already installed in what is supposed to be the final configuration and in the Renton factory, there is a job for the doors team to verify this “final” install and rigging meets drawing requirements. In a healthy production system, this would be a “belt and suspenders” sort of check, but the 737 production system is quite far from healthy, its a rambling, shambling, disaster waiting to happen. As a result, this check job that should find minimal defects has in the past 365 calendar days recorded 392 nonconforming findings on 737 mid fuselage door installations (so both actual doors for the high density configs, and plugs like the one that blew out). That is a hideously high and very alarming number, and if our quality system on 737 was healthy, it would have stopped the line and driven the issue back to supplier after the first few instances. Obviously, this did not happen. Now, on the incident aircraft this check job was completed on 31 August 2023, and did turn up discrepancies, but on the RH side door, not the LH that actually failed. I could blame the team for missing certain details, but given the enormous volume of defects they were already finding and fixing, it was inevitable something would slip through- and on the incident aircraft something did. I know what you are thinking at this point, but grab some popcorn because there is a plot twist coming up.
The next day on 1 September 2023 a different team (remember 737s flow through the factory quite quickly, 24 hours completely changes who is working on the plane) wrote up a finding for damaged and improperly installed rivets on the LH mid-exit door of the incident aircraft.
A brief aside to explain two of the record systems Boeing uses in production. The first is a program called CMES which stands for something boring and unimportant but what is important is that CMES is the sole authoritative repository for airplane build records (except on 787 which uses a different program). If a build record in CMES says something was built, inspected, and stamped in accordance with the drawing, then the airplane damn well better be per drawing. The second is a program called SAT, which also stands for something boring and unimportant but what is important is that SAT is *not* an authoritative records system, its a bullentin board where various things affecting the airplane build get posted about and updated with resolutions. You can think of it sort of like a idiots version of Slack or something. Wise readers will already be shuddering and wondering how many consultants were involved, because, yes SAT is a *management visibilty tool*. Like any good management visibilty tool, SAT can generate metrics, lots of metrics, and oh God do Boeing managers love their metrics. As a result, SAT postings are the primary topic of discussion at most daily status meetings, and the whole system is perceived as being extremely important despite, I reiterate, it holding no actual authority at all.
We now return to our incident aircraft, which was written up for having defective rivets on the LH mid-exit door. Now as is standard practice kn Renton (but not to my knowledge in Everett on wide bodies) this write-up happened in two forms, one in CMES, which is the correct venue, and once in SAT to “coordinate the response” but really as a behind-covering measure so the manager of the team that wrote it can show his boss he’s shoved the problem onto someone else. Because there are so many problems with the Spirit build in the 737, Spirit has teams on site in Renton performing warranty work for all of their shoddy quality, and this SAT promptly gets shunted into their queue as a warranty item. Lots of bickering ensues in the SAT messages, and it takes a bit for Spirit to get to the work package. Once they have finished, they send it back to a Boeing QA for final acceptance, but then Malicious Stupid Happens! The Boeing QA writes another record in CMES (again, the correct venue) stating (with pictures) that Spirit has not actually reworked the discrepant rivets, they *just painted over the defects*. In Boeing production speak, this is a “process failure”. For an A&P mechanic at an airline, this would be called “federal crime”.
Presented with evidence of their malfeasance, Spirit reopens the package and admits that not only did they not rework the rivets properly, there is a damaged pressure seal they need to replace (who damaged it, and when it was damaged is not clear to me). The big deal with this seal, at least according to frantic SAT postings, is the part is not on hand, and will need to be ordered, which is going to impact schedule, and (reading between the lines here) Management is Not Happy.
However, more critical for purposes of the accident investigation, the pressure seal is unsurprisingly sandwiched between the plug and the fuselage, and you cannot replace it without opening the door plug to gain access. All of this conversation is documented in increasingly aggressive posts in the SAT, but finally we get to the damning entry which reads something along the lines of “coordinating with the doors team to determine if the door will have to be removed entirely, or just opened. If it is removed then a Removal will have to be written.” Note: a Removal is a type of record in CMES that requires formal sign off from QA that the airplane been restored to drawing requirements.
If you have been paying attention to this situation closely, you may be able to spot the critical error: regardless of whether the door is simply opened or removed entirely, the 4 retaining bolts that keep it from sliding off of the door stops have to be pulled out. A removal should be written in either case for QA to verify install, but as it turns out, someone (exactly who will be a fun question for investigators) decides that the door only needs to be opened, and no formal Removal is generated in CMES (the reason for which is unclear, and a major process failure). Therefore, in the official build records of the airplane, a pressure seal that cannot be accessed without opening the door (and thereby removing retaining bolts) is documented as being replaced, but the door is never officially opened and thus no QA inspection is required.
This entire sequence is documented in the SAT, and the nonconformance records in CMES address the damaged rivets and pressure seal, but at no point is the verification job reopened, or is any record of removed retention bolts created, despite it this being a physical impossibility. Finally with Spirit completing their work to Boeing QAs satisfaction, the two rivet-related records in CMES are stamped complete, and the SAT closed on 19 September 2023. No record or comment regarding the retention bolts is made.
I told you it was stupid.
So, where are the bolts? Probably sitting forgotten and unlabeled (because there is no formal record number to label them with) on a work-in-progress bench, unless someone already tossed them in the scrap bin to tidy up.
There’s lots more to be said about the culture that enabled this to happened, but thats the basic details of what happened, the NTSB report will say it in more elegant terms in a few years.''
There probably in the mechanics tool box with the cotter pins.
Thanks AnishReddi - this is the most authoritative explanation I have seen, and now, I can understand how it happened.
There was a good interview of Ben Minicucci, CEO of Alaska Airlines, and he reports that they found "many" Boeing aircraft with "loose bolts".
Ben Minicucci said, "“I’m more than frustrated and disappointed, I am angry. This happened to Alaska Airlines. It happened to our guests and happened to our people. And —...
Thanks AnishReddi - this is the most authoritative explanation I have seen, and now, I can understand how it happened.
There was a good interview of Ben Minicucci, CEO of Alaska Airlines, and he reports that they found "many" Boeing aircraft with "loose bolts".
Ben Minicucci said, "“I’m more than frustrated and disappointed, I am angry. This happened to Alaska Airlines. It happened to our guests and happened to our people. And — my demand on Boeing is what are they going to do to improve their quality programs in-house?”
I think EVERY Airline CEO will demand improvements from Boeing.
With all of the attention already paid to Boeing over the last several years, do you think that this is something Boeing can recover from, or will it be sufficient to make management changes?
Quite shocking that the Seattle Times does not refer to Leeham News in a transparent way,t's clearly Leeham's loyal following that allowed this whistle to be blown. The Seattle Times has nothing in this scoop, except maybe a larger audience and questionable ethics.
Maybe worthwhile to update/remove the reference to The Seattle Times and refer to the more accurate and original source.
Leeham News has also independently verified the disclosure with current Boeing...
Quite shocking that the Seattle Times does not refer to Leeham News in a transparent way,t's clearly Leeham's loyal following that allowed this whistle to be blown. The Seattle Times has nothing in this scoop, except maybe a larger audience and questionable ethics.
Maybe worthwhile to update/remove the reference to The Seattle Times and refer to the more accurate and original source.
Leeham News has also independently verified the disclosure with current Boeing employee sources. While the exactitude of the "what" cannot be confirmed (not everyone is a whistleblower) the way it happened (the "how") is apparently an accurate (and scary !) depiction of the poor state of Boeing's and Spirit production lines.
The answer is quite simple. Boeing is a monopoly. With heavy political backing, there is no other option.
Instead of the FTC blocking low level ULCC carriers mergers they should be looking at Boeing and the competition that lead up to a single manufacturer of commercial aircraft in the United States. Doubt there’s much to do about it either.. forced breakup ?
Airbus.
In the US, most political negotiations abroad include the sales of Boeing aircraft
Breakup how?
This would be a King Solomon baby splitting situation.
Breakup as in separate Boeing Defense from Boeing Commercial Aircraft.
Sell the later off to, say, Lockheed for example.
Not saying that this is likely, in any way, but definitely possible.
I don't understand how the maintenance logs could indicate that 4 bolts were not installed in black and white and then how the software even allows that plane to be "checked out" and returned to the customer with 4 bolts missing. It would be one thing if a mechanic just lied and checked off that he did something and then forgot to actually install the bolts. That's human error that can't be eliminated. This could've been flagged by the software...
I'm guessing it's a shortcoming of their reporting system. If the plane had an actual door, they would have simply opened the door, replaced the seal, have QA sign off on the work, and then close the door, without having the inspector actually confirm that they indeed closed the door. If they had to remove the entire door for whatever reason, the reinstall would have to be inspected.
It was probably logged as though the...
I'm guessing it's a shortcoming of their reporting system. If the plane had an actual door, they would have simply opened the door, replaced the seal, have QA sign off on the work, and then close the door, without having the inspector actually confirm that they indeed closed the door. If they had to remove the entire door for whatever reason, the reinstall would have to be inspected.
It was probably logged as though the plane had a door to be opened, and not a plug to be removed. Just horrible quality management, not that any of us are surprised anymore.
It's not just that. The other problem is that a regular airplane door, when closed, is also by design secured such that it will not open at altitude.
The fake doors are not. They are designed with springs on their bottom hinges that are constantly trying to push the door open even when the door is closed, so you have to put the bolts in to stop that.
No bolts and the door WILL eventually open itself.
How stupid a design is that?
Maybe the mechanic never learned to read in school, wasn't ever tested for reading ability (because testing is bad), and couldn't fill out the form.
In regards to your comparisons of whether it’s a design issue of the plane vs a quality control issue.. are we supposed to accept that 4 bolts—whether loose or missing—results in the whole door panel flying off? To me that sounds like both a quality AND a design issue. We’ve been down this road with the MAX. Whether it’s software like MCAS or physical nuts and bolts, an isolated single point of failure that can...
In regards to your comparisons of whether it’s a design issue of the plane vs a quality control issue.. are we supposed to accept that 4 bolts—whether loose or missing—results in the whole door panel flying off? To me that sounds like both a quality AND a design issue. We’ve been down this road with the MAX. Whether it’s software like MCAS or physical nuts and bolts, an isolated single point of failure that can lead to catastrophic failure sounds like a design flaw to me. How can a couple bolts determine if entire fuselage is compromised and potentially killing passengers? Would a submarine or ship allow 4 bolts to determine if the hull is compromised and gets flooded?
But let’s assume that 4 bolts can be allowed to lead to such a failure. Wouldn’t the lack of quality control on such important bolts mean severe consequences? This is just as bad as MCAS in my opinion because a global manufacturer is basically making planes with duct tape for parts that determine life or death for passengers..
If it's Boeing, I ain't going!
The NTSB and Boeing undoubtedly both know this which is why the inspections were required of the 737-900ERs which have the same door design but it is becoming increasingly obvious that this is a manufacturing and quality control error at Boeing which is happening now and didn't happen 10 or more years ago when most 737-900ERs left the factory. Delta has some of the youngest and last 737-900ERs that were built but they were all...
The NTSB and Boeing undoubtedly both know this which is why the inspections were required of the 737-900ERs which have the same door design but it is becoming increasingly obvious that this is a manufacturing and quality control error at Boeing which is happening now and didn't happen 10 or more years ago when most 737-900ERs left the factory. Delta has some of the youngest and last 737-900ERs that were built but they were all delivered before covid.
Spirit (SPR) is just part of a long production cycle that begins with suppliers to both Boeing (BA) and SPR and culminates w/ the Boeing seal of approval before the plane is delivered.
Ultimately, BA is responsible for ensuring the quality of the product it delivers which means finding and correcting whatever problems exist anywhere in the process before a plane gets to Boeing's factories.
A single day of production standdown won't fix anything unless BA also reworks the processes that allow production faults to happen in the first place.
It is good that the NTSB is getting to the core of the issue. It is now up to the FAA to come up w/ the right processes to inspect for any problems newer 737s might have. So far, inspections indicate these door manufacturing problems are not long-standing.
If this is true, it is truly horrifying as the repairs performed by Boring could not be trusted. I recalled crash of Japan Airlines flight 123 in 1985 which killed 520 people on board of B747 caused by the inadequate repair of rear pressure bulkhead by Boeing.
just for clarification, but the repair was done incorrectly by JAL, not Boeing; the repair wasn't Boeing's approved methods of repair. Subsequently, a JAL maintenance manager has committed suicide.
https://en.wikipedia.org/wiki/Japan_Air_Lines_Flight_123#Investigation
According to NYT article (Sep 8 1985) referred in that wiki entry:
The Boeing Company acknowledged Friday that it had made faulty rear-cabin repairs in 1978 on a Japan Air Lines Boeing 747 that crashed in Japan last month, killing 520 of the 524 people on board.
But the company added that further analysis was needed ''to determine whether this repair contributed to the accident.'' It was the worst single-plane crash in history.
According to this very same Wiki article, the repair was done by Boeing, not JAL:
"... The subsequent repair of the bulkhead did not conform to Boeing's approved repair methods. For reinforcing a damaged bulkhead, Boeing's repair procedure calls for one continuous splice plate with three rows of rivets.[25] The Boeing repair technicians, however, had used two splice plates parallel to the stress crack.[26][3] Cutting the plate in this manner negated the effectiveness of...
According to this very same Wiki article, the repair was done by Boeing, not JAL:
"... The subsequent repair of the bulkhead did not conform to Boeing's approved repair methods. For reinforcing a damaged bulkhead, Boeing's repair procedure calls for one continuous splice plate with three rows of rivets.[25] The Boeing repair technicians, however, had used two splice plates parallel to the stress crack.[26][3] Cutting the plate in this manner negated the effectiveness of one of the rows of rivets, reducing the part's resistance to fatigue cracking to about 70% of that for a correct repair. The post-repair inspection by JAL did not discover the defect, as it was covered by overlapping plates..."
The original source reports that the responsibility and work were done by Spirit. Spirit was responsible for delivering the fuselage and plug door. That there was a defect in the seal that requires removing the plug door to repair. This was done by Spirit including replacing the plug door (incorrectly)
The Boeing failure is that their system didn't record the door removal and then there was no inspection required of the door replacement.
Boeing is...
The original source reports that the responsibility and work were done by Spirit. Spirit was responsible for delivering the fuselage and plug door. That there was a defect in the seal that requires removing the plug door to repair. This was done by Spirit including replacing the plug door (incorrectly)
The Boeing failure is that their system didn't record the door removal and then there was no inspection required of the door replacement.
Boeing is ultimately responsible but the underlying errors were by Spirit. It doesn't look good in any event